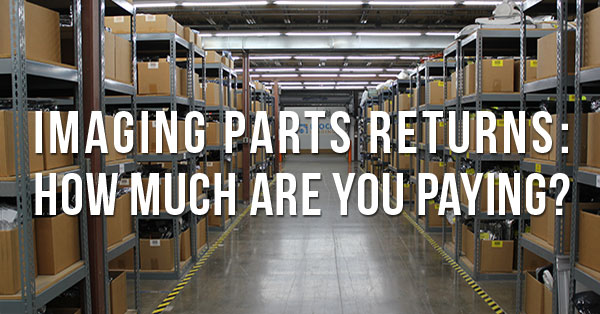
April 19, 2019 : 2 min read
The Hidden Cost of Medical Imaging Parts: Returns
After working closely with countless customers purchasing imaging parts all over the world, I often find there is limited understanding of just how much money can be lost in the returns process. Returns-not-needed, lost exchanges, and late exchanges are an enormous hidden expense in the medical imaging parts industry.
If this leaves you wondering how much you could be losing, consider these questions about the current state of your parts return process:
Do you know what your organization spends on returns?
Usually, the answer is "no". Sometimes, I'll hear a parts buyer say, "We have some vendors who don't charge us restock fees." Well, yes and no. You may have a certain amount of parts you can return without paying a restock, but what about lost exchanges? Late exchanges? The reality is you're paying for a bad return process. And it's probably more than you think.
Is there accountability to return exchanges?
Again, the answer is usually "no". Even if your imaging engineers logically know they need to send back an exchange part, in the absence of accountability it's easy for the "tyranny of the urgent" (i.e. their next service case) to keep them from closing this important loop in the parts buying process. When the rad technician finds the open box with the old part in it under a table in four months, it's just too late. You've already paid a fee.
Do you train and remind your engineers to use RMAs?
More and more imaging parts companies are aggressively requiring “return materials authorizations” (RMA) for returns that are not exchanges (part not needed, part defective, etc.). Sometimes an RMA is a piece of paperwork, sometimes it's a reference number. In any case, reaching out to your vendor and getting an RMA means that you have notified them of your intent to return a part and your reason for returning it.
If your engineers don't obtain and use RMAs when they make non-exchange returns, you're probably not getting the credit back that you deserve. The vendor is left to assume that the part they get back is an exchange. They'll process and restock it like an exchange, and you'll be billed the full price. With a little training and periodic refreshers on RMA use, your engineering team could save you significant dollars in restock fees and mistaken billing.
Tips to save on medical imaging parts returns
Measure the total restock fees and lost/late fees by engineer and facility. You'll find that one team member or one facility is 80% of your returns expense. The could mean there is an opportunity for more training: Maybe it will be technical training, maybe it will returns process training, but either way, the investment will be well worth it!
Have an admin team member follow up on exchanges due. This is one reason why centralized imaging procurement is so valuable, but regardless of who is buying imaging parts for you today, have a member of your team help to hunt down lost parts!
Get RMAs from your vendors and archive tracking information. When there is a dispute about whether a part was returned, having the tracking number can make a difference of thousands of dollars on a single transaction!
The Takeaway
If your organization is struggling with restock fees and how to avoid them, we'd love to help! Block Imaging has designed an easy to use process for making sure your engineers have everything they need to get parts sent back easily! Contact us to set up a time to review how your team is buying (and returning) imaging parts.
Contact Us
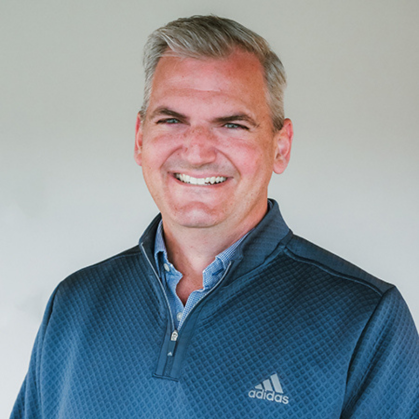
Jason Crawford
Jason Crawford is the President of Block Imaging. Jason’s biggest interests involve anything that brings new insight into investing in people and building high-trust relationships. He believes that excellence in both of these areas can build the best team for delivering on the needs of customers. Outside of work, Jason enjoys spending time with his wife and three amazing kids who love to play board games.